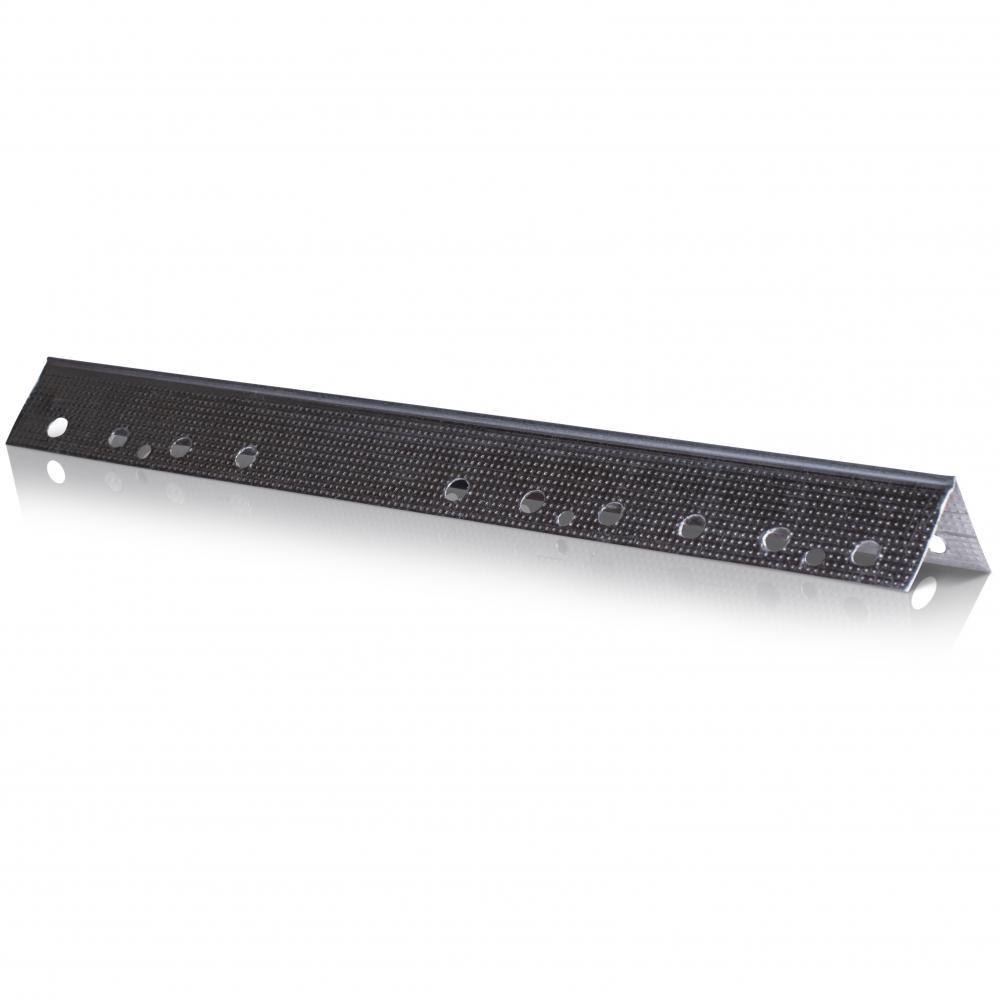
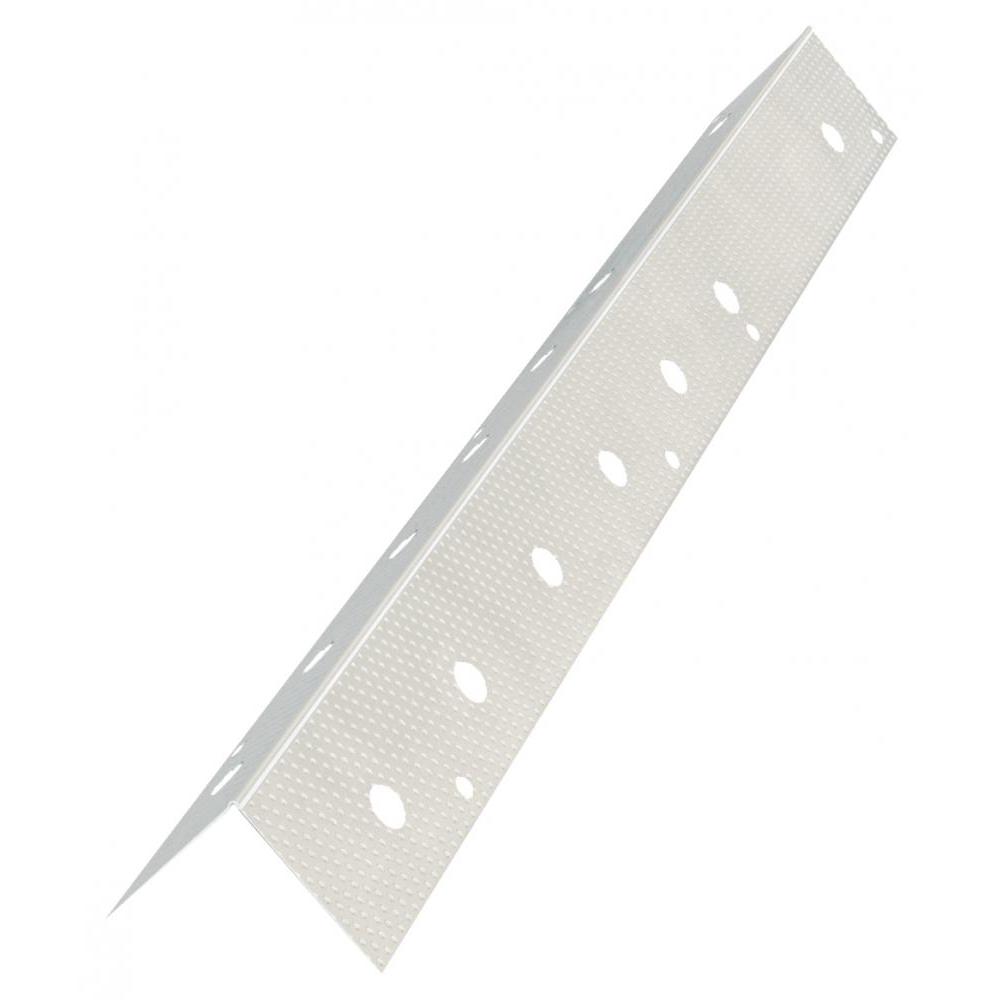
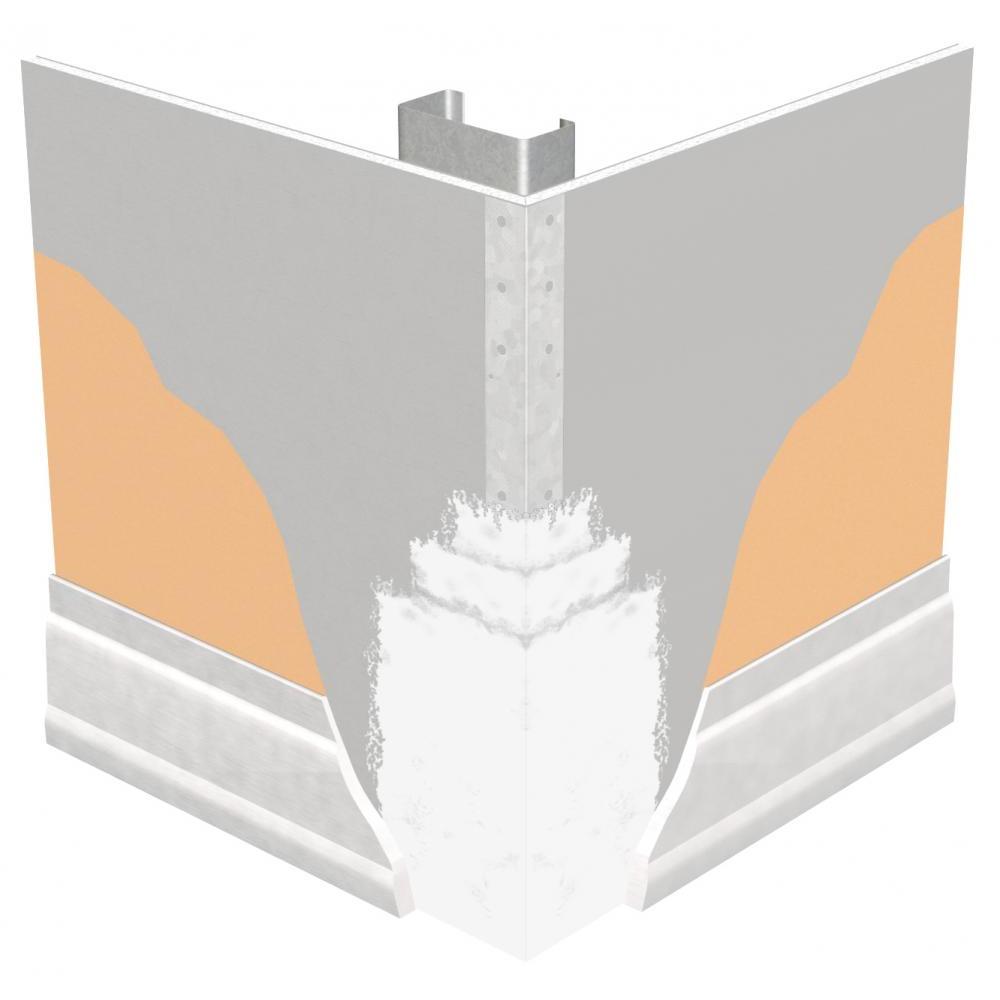
Hot-Dipped METAL CORNER BEAD
Quicksilver™ corner bead is used to achieve outside 90° corners.
ClarkDietrich Quicksilver flanges are deeply knurled and perforated for excellent joint compound adhesion. This product combines a unique manufacturing process with specially enhanced galvanized steel to provide consistent finishing. This traditional drywall finishing product is nailed, stapled, screwed or clinched into place.
- Hot dipped galvanized coating for corrosion protection
- Metal reinforcement for drywall corners
- Exposed nose resists impact and forms a screed for finishing
Material: 0.0125 min thickness, G30 galvanized
Product Data & Ordering Information
Product code | Width | Length | Pcs./Ctn. | Ctns/Skid |
---|---|---|---|---|
CBS | 1-1/4" x 1-1/4" | 6' 9" | 75 | 48 |
1-1/4" x 1-1/4" | 6' 10" | 75 | 48 | |
1-1/4" x 1-1/4" | 7' | 72 | 48 | |
1-1/4" x 1-1/4" | 8' | 63 | 48 | |
1-1/4" x 1-1/4" | 9' | 56 | 48 | |
1-1/4" x 1-1/4" | 10' | 50 | 48 | |
1-1/4" x 1-1/4" | 12' | 42 | 48 |
INSTALLATION
Metal corner beads can be installed using a variety of methods. You may choose to do a combination of all three.
For regular metal corner bead, the drywall does not need to be set back.
Method 1: Staples
- Measure the wall height and subtract ½”. Measure and cut the corner bead using aviator snips. Dry fit to ensure accuracy.
- Position the bead on the corner and staple each mud flange every 6” to 10” with ½” staples.
- Using an 8” taping knife, apply the first coat of joint compound to the surface of the corner bead. The use of lightweight or setting-type compound in this step will reduce shrinkage and speed up drying time. Let this dry completely, for several hours or overnight.
- Using an 8” or 10” taping knife, apply a light finish coat of joint compound. Feather the compound beyond the previous coat. The use of all-purpose or topping compound will make for a more durable finish. Let this dry completely, for several hours or overnight.
- Sand lightly with 120 grit sandpaper.
Method 2: Screws or Nails
- Measure the wall height and subtract ½”. Measure and cut the corner bead using aviator snips. Dry fit to ensure accuracy.
- Position the bead on corner and fasten the bead with screws or nails using the smaller nail holes on each mud flange.
- Using an 8” taping knife, apply the first coat of joint compound to the surface of the corner bead. The use of lightweight or setting-type compound in this step will reduce shrinkage and speed up drying time. Let this dry completely, for several hours or overnight.
- Using an 8” or 10” taping knife, apply a light finish coat of joint compound. Feather the compound beyond the previous coat. The use of all-purpose or topping compound will make for a more durable finish. Let this dry completely, for several hours or overnight.
- Sand lightly with 120 grit sandpaper.
Method 3: Clinch-On Tool
- Measure the wall height and subtract ½”. Measure and cut the corner bead using aviator snips. Dry fit to ensure accuracy.
- Position the bead on the corner. Place the clinch-on tool over the bead.
- Hit the tool with a rubber mallet to crimp the bead to the corner, repeating every 8” to 10” for optimum fastening.
- Using an 8” taping knife, apply the first coat of joint compound to the surface of the corner bead. The use of lightweight or setting-type compound in this step will reduce shrinkage and speed up drying time. Let this dry completely, for several hours or overnight.
- Using an 8” or 10” taping knife, apply a light finish coat of joint compound. Feather the compound beyond the previous coat. The use of all-purpose or topping compound will make for a more durable finish. Let this dry completely, for several hours or overnight.
- Sand lightly with 120 grit sandpaper.
Documents
Code Approvals & Performance Standards
- ASTM C1047 Standard Specification for Accessories for Gypsum Wallboard and Gypsum Veneer Base
- SDS For ASTM A653 Steel Finishing Products For Interior Finishing and Exterior Finishing
PRoduct submittal SHeets
Click the below Product Code to view Submittal/Tech Datasheet.
Product Code | Description |
---|---|
CBS | Quicksilver Corner Bead |
ClarkDietrich SubmittalPro®
Submittal sheets for the exact product you're looking for can be created by using ClarkDietrich's SubmittalPro® Product Submittal System.
- Contact ClarkDietrich Technical Services at 888-437-3244 for any questions about creating product submittals or using SubmittalPro.